Industrial Hygiene Essentials: Key Practices for Managing Workplace Hazards
Industrial hygiene has been a key focus for industry leaders since the early 1900s. In today’s rapidly evolving and fast-paced industries, the importance of planning and implementing effective industrial hygiene practices is more critical than ever. Organizations must prioritize the health and safety of everyone within their employ by planning, implementing, and monitoring effective hazard control management. Within industries such as mining, manufacturing, petroleum refining, and construction, the development and execution of industrial hygiene practices can be extremely complex and challenging. From reducing exposure to airborne toxins and hazardous combustible dust to chemical fumes and high winds, this blog will explore key industrial hygiene practices to help make your workplace a healthier, safer environment.
What is Industrial Hygiene?
Industrial hygiene is defined as the “art and science dedicated to the Anticipation, Recognition, Evaluation, Control, and Confirmation of protection from those environmental stressors in, or arising from, the workplace that may result in injury, illness, impairment, or affect the well-being of workers and members of the community 1 ”.
Background
Employee health and safety is of paramount importance in all workplaces. There are many organizations around the world (e.g. OSHA) dedicated to the protection of workers from work- related exposure to hazardous materials, health risks and injury. In 2023 and 2024, the International Labour Organization provided startling and devastating statistics regarding global worker health and safety 2. The image below illustrates some of the impacts of occupational hazards.
Adapted from International Labor Organization https://www.ilo.org/topics-and-sectors/safety-and-health-work
It is obvious from the numbers, that continuing to plan and implement occupational health and safety measures remains of the utmost importance for industries around the globe. In recent years, with the help of industrial hygienists, many businesses have incorporated industrial hygiene programs focused on safeguarding their employees from hazardous work environments in an effort to protect them from injury, health risks and other safety issues.
Types of Workplace Hazards
There are a plethora of individual health and safety risks that employees may encounter on a daily basis in the workplace. Some of the more common hazards and risks can be broadly categorized according to the following 2 :
- Biological hazards: Exposure to organic material such as bacteria, mold, biological fluids, viruses, and fungus that may affect the well-being of workers.
- Chemical hazards: Exposure to chemical such as mercury, cyanide, sulfuric acid, and other solvents. Chemical exposure may be encountered through skin absorption, vapour and fume inhalation, or ingestion 3,4. Airborne chemical hazards may present as mists, vapors, gases, fumes, or solids (e.g. harmful dust) 4.
- Physical hazards: Exposure to extreme temperatures, noise, radiation, heights and strong winds are examples of potential physical hazards in a workplace.
- Psychosocial hazards: Exposure to high stress, excessive workload, high work pace, harassment and a toxic corporate culture are a few of the examples of stressors that negatively affect workers’ mental health in the workplace.
- Ergonomic hazards: Repetitive strain injuries, improper workstation setup and manual lifting may result in injury or safety-related issues for employees.
We will explore specific examples of mitigation and prevention strategies that workers and employers can implement to reduce workplace hazards a little further on in the blog after we have gained more understanding on the principles of industrial hygiene practices that should be adhered to.
Key Industrial Hygiene Practices
Industrial hygiene practices are categorized into 3 key areas of focus. Each area plays a fundamental role in reducing and addressing potential and realized safety concerns within the workplace. Hygiene practices generally involve monitoring and risk assessment, implementation of control measures, and maintaining and fostering established practices. Let’s delve a little deeper into each of these focus areas.
1. Monitoring & Risk Assessment
Gaining insight and understanding of potential risks that workers may encounter within an organization or industry provides employers with valuable information to begin planning or to improve current health and safety measures. Government agencies, such as the Occupational Safety and Health Administration (OSHA) and the National Institute for Occupational Safety and Health (NIOSH), as well as other agencies in multiple other countries provide published guidelines, assessment tools, training programs and other resources for organizations to improve worker safety and reduce health hazards in the workplace.
Conducting a thorough risk assessment provides employers with useful data to identify and evaluate risk hazards and levels. In collaboration with industrial hygienists and consultants, employers are then better equipped to develop and implement control measures to mitigate the threats identified. During these worksite analyses, the jobs and work stations that are the sources of the potential problems are brought to light. It has been determined that the most effective analyses are those that include all jobs, operations and work activities 4. Data that is gathered and evaluated to determine potential hazards generally includes information found in safety incident reports, inspections, worker feedback and identified exposures 4. Usually, a risk analysis is then conducted to determine the severity and likelihood of the potential event from occurring or recurring. Risk levels may then be quantified through risk assessment tools such as matrices or scoring systems.
2. Implementing Control Measures
Once the data gathered from the risk assessment has been collated, analyzed and reviewed, it is time for employers to take corrective action. In the world of occupational health and safety there are a few recognized ways to control hazards: engineering controls, work practice controls and administrative controls 4. Each one of these controls focus on a different aspect of the work environment. Engineering controls address health and safety issues by removing the risk altogether or isolating workers from it 4. An example of engineering controls as it pertains to industrial hygiene would be incorporating a wind fence on a mining site as part of a dust management strategy for dust control and mitigation.
Work practice controls tackle how a specific task is completed. For instance, implementing or improving ventilation in high-risk areas to reduce toxic fumes or vapour and cleaning up spills immediately are examples of work practice controls.
Finally, administrative controls focus on functions that are related to managing work processes or operations as they pertain to industrial safety. Examples of administrative controls include rotating workers between different tasks and areas to reduce exposure to a hazard, or establishing guidelines and standard operating procedures for handling dangerous chemicals.
In addition to the three main control measures for industrial hygiene discussed above, personal protective equipment (PPE) such as gloves, masks, ear plugs and hard hats should be implemented in situations where they are warranted for worker protection.
3. Maintaining & Fostering Industrial Hygiene Practices
In order to ensure the efficacy of implemented corrective and control measures for industrial safety a series of checks and balances should be put in place by the organization. Conducting essential. Examples of indicators to track may include number of safety incidents, employee absenteeism and near misses. It is also recommended to conduct regular reviews of risk assessments and update safety protocols when required.
Ongoing training and education are also an integral part of ensuring optimal health and safety outcomes within the work environment. Data gathered from risk assessments can be used to identify appropriate training and educational needs for employees. Organizations have a responsibility to foster a culture of safety and take action to ensure that employees are aware of and properly trained to handle workplace related risks or emergencies. Huddles and regular check ins with workers may be of benefit to help cultivate this culture and encourage open communication regarding safety concerns.
Tips on Managing Workplace Hazards
We have looked at how common workplace hazards and general industrial safety practices are categorized and applied as it pertains to workplace safety. The following table provides some practical examples of specific measures that may be taken to mitigate risks within each category of hazard.
The Top Ten Most Frequently Violated Occupational Safety and Hazard Standards
Even with the extensive resources, policies and procedures available and enacted legislation, many organizations still fail to meet the required standards to prevent and protect workers from injury. OSHA tracks regulatory violations and other statistics with regard to employee safety and posts the results on their website. According to OSHA statistics, the top ten safety standards that were cited for non-compliance in inspections from October 2022 to September 30, 2023 were17 :
- Fall protection in construction
- Hazard communication in general industry
- Ladders in construction
- Scaffolding in construction
- Powered Industrial Trucks in general industry
- Control of Hazardous Energy in general industry
- Respiratory industry in general
- Fall Protection Training in construction
- Eye and Face Protection in construction
- Machinery and Machine Guarding in general industry
These safety protocols help to protect workers from preventable occupational injury and death. For more information on where your particular industry ranks with regard to OSHA standards visit the OSHA website at https://www.osha.gov/ords/imis/industryprofile.html.
The Future of Industrial Hygiene
With an ever-increasing focus on improving safety in the workplace, the landscape of industrial hygiene is trending in a positive direction. The emergence of smart PPE in the form of hard hats with proximity sensors and location trackers as well as using predictive analytics 5 for safety are examples of recent shifts that are occurring within the safety industry.
Smart PPE incorporates sensors and wearable devices to monitor location, fatigue levels and vital signs 6. These sensors allow companies to monitor employee health and safety in real time which can reduce the occurrence of serious workplace injury or death. In some instances, smart PPE can alert workers to hazardous conditions such as when they are close to dangerous situations or by providing fall detection technology 6.
Summing it Up
Prioritizing industrial hygiene practices is essential for maintaining a safe and healthy workplace. As industries continue to evolve and face new challenges, the role of industrial hygiene in protecting workers from hazardous exposures has become more critical. Through effective risk assessments, control measures, and ongoing training, organizations can significantly reduce the potential for accidents, injuries, and illnesses. The integration of advanced technologies, such as smart PPE and predictive analytics, is further enhancing the ability to monitor and mitigate risks in real time. As we look to the future, maintaining a strong commitment to industrial hygiene will be key to ensuring a safer, more sustainable work environment for all employees.
References and Additional Reading Materials:
1. https://www.aiha.org/about-aiha Accessed November 27, 2024
2. International Labour Organization “Safety and Health at Work” https://www.ilo.org/topics-
and-sectors/safety-and-health-work Accessed November 27, 2024
3. International Labour Organization “ Chemical Safety and the Environment”
https://www.ilo.org/topics/safety-and-health-work/chemical-safety-and-environment
Accessed November 27, 2024
4. OSHA Office of Training and Education “Industrial Hygiene”
https://www.osha.gov/sites/default/files/training-library_industrial_hygiene.pdf Accessed
November 27, 2024
5. Top Trends in OEHS https://www.aiha.org/blog/top-trends-in-oehs Accessed November
28, 2024
6. Brenneman, K., “The Role of Smart PPE in Modern Manufacturing” Paint and Coating
Equipment. December 14, 2023. https://www.pcimag.com/blogs/14-pci-
blog/post/112003-the-role-of-smart-ppe-in-modern-manufacturing Accessed November
28, 2024
7. International Labour Organization “Technical Guidelines on biological hazards in the
working environment” Meeting of Experts for the tripartite validation of the technical
guidelines on biological hazards Geneva, 20-24 June 2022 – Accessed Jan 6, 2025
8. Occupational Safety and Health Administration “Chemical Hazards and Toxic
Substances” https://www.osha.gov/chemical-hazards/controlling-exposure Accessed
Jan 6, 2025
9. Canadian Centre for Occupational Health and Safety “Hazard and Risk”
https://www.ccohs.ca/oshanswers/hsprograms/hazard/hazard_control.html Accessed
Jan 6, 2025
10. Safety Line “Workplace Hazards Series: Physical Hazards”
https://safetylineloneworker.com/blog/workplace-hazards-physical-hazards Feb 16,
2024. Accessed Jan 6, 2025.
11. Canadian Centre for Occupational Health and Safety “Teaching Tools – Physical
Hazards” https://www.ccohs.ca/teach_tools/phys_hazards/phys_intro.html Accessed Jan
6, 2025.
12. Canadian Centre for Occupational Health and Safety “Psychological Health and Safety
Program – Controlling Psychosocial Hazards”
https://www.ccohs.ca/oshanswers/psychosocial/phs/phs_controllinghazards.html
Accessed Jan 6, 2025.
13. Safe Work Australia “Managing psychosocial hazards at work – Code of Practice” July
2022. https://www.safeworkaustralia.gov.au/sites/default/files/2022-
07/model_code_of_practice_-_managing_psychosocial_hazards_at_work.pdf Accessed
Jan 6, 2025.
14. Occupational Safety and Health Administration “Ergonomics Solutions to Control
Hazards” https://www.osha.gov/ergonomics/control-hazards Accessed Jan 6, 2025.
15. World Health Organization https://www.who.int/news/item/17-09-2021-who-ilo-almost-2-
million-people-die-from-work-related-causes-each-year Accessed August 8, 2024
16. Pega, F., Al-Emam, R., Cao, B., et al “New global indicator for workers’ health: mortality
rate from diseases attributed to selected occupation risk factors” Bulletin World Health
Organization 2023;101:418-430Q doi:http://dx.doi.org/10.2471/BLT.23.289703 Accessed
Jan 6, 2025.
17. OHSA “Top 10 Most Frequently Cited Standards”
https://www.osha.gov/top10citedstandards Accessed Jan 6, 2025.
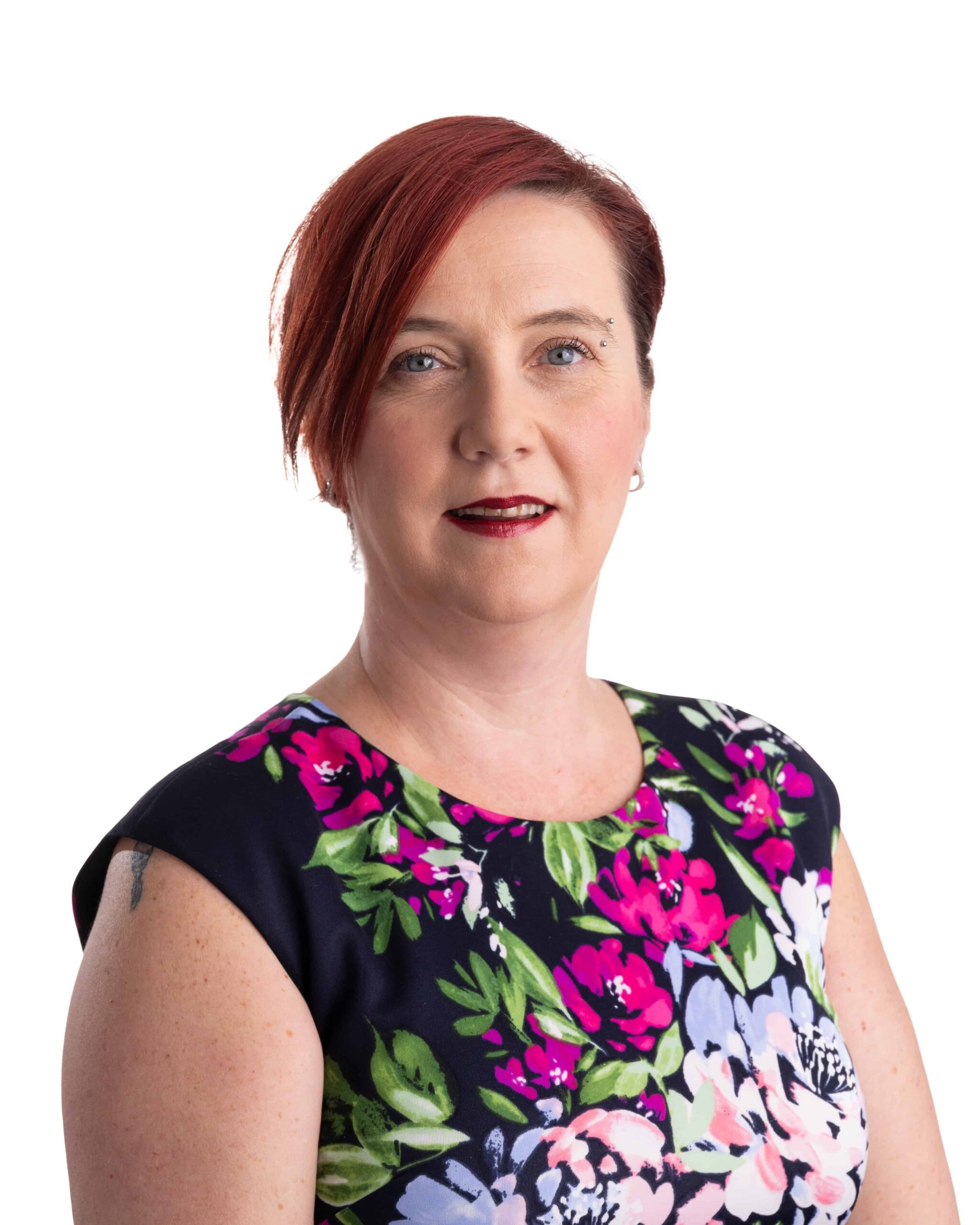
Claire Cowie is a seasoned Quality Assurance Manager with over two decades of experience in healthcare and manufacturing. Her career began in pharmacy, where she led teams and honed her skills in quality management systems. As she transitioned to the manufacturing sector, her unique background combines a deep understanding of policy and quality assurance with a keen eye for quality control.
Claire has been instrumental in implementing and cultivating a comprehensive quality control program within WeatherSolve Structures. She has successfully integrated her pharmaceutical background with manufacturing best practices, particularly in areas such as Good Manufacturing Practices (GMP) and ISO 9001 standards. Her unique blend of experience continues to drive innovation and excellence in her role.