Choosing the Right Fabric for Custom Wind Fences: Key Considerations for Performance and Longevity
When it comes to designing and installing effective custom wind fences, selecting the right barrier material is critical. Wind fences are erected porous structures that play a key role in mitigating wind and dust in a multitude of settings. From mining and industrial sites to orchards and sports venues, custom wind fences offer versatile solutions to many environmental control and weather-related issues. Custom wind fence design engineers take into account a virtual grocery list of criteria that must be considered during the design and development stages. One of these many considerations is the classification and structural properties of the material that is used. Custom wind fences typically use porous fabrics as a barrier, however; not all fabrics are created equal and determining the right textile is key as it can significantly impact fence effectiveness, longevity, and overall return on investment.
In this blog, we will explore the highly specialized world of custom wind fence fabrics. We will cover topics ranging from material options and their suitability for different environmental conditions to various fabric structures and their associated risks and benefits. Whether you’re managing an industrial facility, overseeing agricultural operations or looking to further your knowledge on the intricacies of dust suppression strategies, understanding these considerations will help you make informed decisions to ensure your wind fence meets both functional and site-specific requirements.
Wind Fences: The Basics
The primary function of a wind fence is to reduce wind velocity in a specific area to provide protection from the impacts of strong winds and gusts while controlling fugitive dust. Wind fences are constructed by erecting a porous material to act as a barrier against wind and reduce dust in a plethora of environments such as bulk material handling, mining, manufacturing, and solar farms. The porous barrier reduces the velocity of wind and significantly diminishes dust by two key modes: upwind fences and downwind fences. Upwind fences reduce the velocity of incoming winds thereby preventing dust particle uptake, whereas downwind fences “catch” dust that is still in motion. As wind directions change, an upwind fence may become a downwind fence, and vice versa. The benefits of implementing or integrating a wind fence into current dust management plans are wide-ranging and have been studied extensively. For further information on wind fences reach out to our experts directly at info@weathersolve.com or by phone at 1-800-749-2201. We’d love to hear from you.
Custom Wind Fence Fabric Properties & Structure
The field of fabric structure is complex with many nuances and variants. As it pertains to custom wind fences, the structural properties of a fabric provide information for engineers and designers to determine the suitability of a fabric for a particular application. Let’s take a quick look at some of the properties of wind fence fabric that influence fabric performance.
Among the properties that are evaluated during custom wind fence design and development, the porosity of the factor is perhaps one of the most critical in determining the efficiency of a wind fence6. Consideration of porosity is of importance as different values will affect different outcomes depending on the type of application. For instance, the optimal fabric porosity for a fence that is designed primarily for dust control will differ from the optimal fabric porosity used in a fence for a sports venue, agricultural application, or hail protection. There are two key categorizations of porosity: visual and aerodynamic. Aerodynamic porosity is what the wind “sees”, in other words the structural openness of a fabric which determines how much wind can pass through dependent on the construction of the fabric holes. Aerodynamic porosity is typically less than visual porosity.
Visual porosity is what we see – the ratio of open area to the total area of the fabric. To add to this, visual porosity changes based on the angle to the sun. For wind fences used in sports venues, visual porosity must be considered.
The most effective fabric porosity for dust control has been shown to be between 30 – 50%. The porosity of the fabric, in addition to fence height and length, also impacts total sheltered area and structural loads. Wind fence panels constructed with 24% porous fabric will have greater structural loads than those found with 47% porous fabric. This can profoundly affect overall cost as the bulk of a wind fence investment is due to the supporting steel poles and foundations. The porosity of the fabric for wind fences also differs dependent on the modality of the wind fence. Downwind fences catch dust that is still in motion and therefore lower porosity allows less dust to pass through, however; the lower the porosity, the higher the cost of the fence due to increased structural loads. Based on WeatherSolve’s extensive experience, the best compromise to reduce dust and keep costs reasonable is to use upper fence fabrics with 34-40% porosity. The lower part of a fence is then constructed of more solid fabrics and a low block wall to maximize dust suppression. It is important to note that the majority of dust is less than a metre above ground level so having more solid fabrics near the bottom of a downwind fence is preferred. For incoming turbulent winds, 47% porous fabric is generally a good choice for an upwind fence as it provides both good shelter and filtering properties.
In general, there are two types of wind fence fabrics used for – knitted or woven. Understanding the differences between these two types of textiles can help when determining which fabric is right for your wind fence.
Knitted fabric is created by inter-looping the same yarn across itself to form a stretchy textile. Woven fabric on the other hand is made by interlacing two distinct yarns at ninety-degree angles – warp and weft. The warp yarns run longitudinally along the fabric while the weft yarns run transversely across the fabric. An easy way to remember this is “weft to wight”. In addition, woven fabrics tend to have less elasticity initially than knitted fabrics as they only stretch along the bias, but tend to be more consistently elastic over time. Knitted fabrics on the other hand are stretchy both lengthwise and widthwise, however; if the fabric is stretched lengthwise it will simultaneously narrow widthwise and vice versa. Knitted fabrics intersect and form a pseudo loose “knot” at each intersection. Over time, knitted fabrics tend to sag as the fabric becomes looser and less stretchy as a result of these loose “knots” continually tightening until they pull up nearly solid. This process can take some time depending on the loading and frequency of it that the fabric has undergone.
The overall weight and weave type of the woven fabric also influences how the wind fence panel will perform. For woven fabrics, the overall weight of the fabric depends on the weight (or thickness) of the individual yarns and the number of yarns per inch. Weave type affects the performance of the fabric – for instance, plain weave (yarns weaved over and under each other) will have different properties than leno weave (adjacent warp threads twisted around the weft thread) as leno weave will resist loosening over time and allow for greater controlled porosity. Heavier fabrics tend to have greater wind resistance, strength, and durability. Lighter fabrics reduce the structural load on the wind fence but allow more wind to pass through and are less strong and durable. Specifically, when it comes to knitted and woven fabrics, a knitted fabric needs to be substantially heavier than a woven fabric to demonstrate the same strength.
There are a number of differences in the way knitted and woven fabrics perform as it pertains to wind fences. One major difference is that knitted fabrics tend to unravel or “run” when the inter-looping yarn is damaged. Consider the following possible scenario. A large bird flies into one of the fabric panels of a wind fence, or a vehicle passes too close to the fence, and a portion of the yarns are damaged causing a hole in the fabric. Typically, a knitted fabric that is suitable for a wind fence panel will unravel or “run” causing the hole to become substantially larger and. Tighter knitted textiles with more interconnected yarns are much more stable and would reduce the extent of the unravelling, however; they are generally too dense for use as wind control.
Should the same situation occur with woven fabric, the size of the damaged area usually remains the same due to the warp and weft yarns acting independently of each other. In a large number of cases, and dependent on the severity of the damage, the fence panel constructed from woven fabric remains operational whereas the panel constructed from knitted fabric may need to be replaced.
For wind fences that utilize a stress-release clip system that releases during extreme storms such as those designed and implemented by the industry experts at WeatherSolve Structures, woven fabric is essential to the release system. During extreme weather events, the stress release system prevents high loads from compromising structural integrity of the fence support structure. When the tension on the panel reaches a specific value, highly specialized clips operate in a zipper-like fashion to release the bottom of the wind fence panel while the top of the panel remains in position for safety reasons. The specific value is determined based on the and requires accurate calculation which is not feasible with the use of knitted textiles. Should a wind fence panel be released due to an extreme weather event, the fence panel can be returned to full working order almost immediately by simply replacing the stress release clips. Wind fences constructed without proven stress release systems may experience structural support or foundational failure due to excessive loads on the panel or incur irreparable panel damage resulting in a multitude of panels requiring complete replacement – all costing both precious time and money. For more information, read our blog on stress release systems for wind fence panels.
In addition to the structural properties of wind fence fabrics, the material composition of the fabric must also be considered. There are many types of textiles used to construct wind fence panels including polyethylene, polypropylene and polyester to name a few. Each of these fabrics vary slightly with regard to strength, UV resistance and other properties. For instance, polyester is generally more expensive than polypropylene or polyethylene. All fabrics show good abrasion, flame and UV resistance and are stable at high and low temperatures. Although available in various colours, fabrics are generally carbon black as this provides the least expensive UV inhibition with the least effect on fabric properties such as flame resistance.
It is plain to see that there are many complexities and nuances associated with wind fence textiles. The physical and mechanical properties of these fabrics impact everything from fence performance and efficacy to aesthetics and overall cost. The trusted experts at WeatherSolve Structures are here to walk you through each step of the way to ensure that your wind fence meets the specific, unique requirements of your site to ensure optimal effectiveness with the greatest return on investment.
Selecting the right fabric for custom wind fences is an important decision that directly impacts the effectiveness, durability, and cost efficiency of the barrier. Understanding the nuances of fabric properties such as aerodynamic porosity, material composition, and the structural differences between knitted and woven fabrics allows stakeholders to make informed choices tailored to specific site environmental and operational needs. Whether the goal is to control dust, reduce wind velocity, or protect infrastructure, using the right textile ensures optimal performance and longevity of wind fences. With considerations ranging from aerodynamics to damage resistance, custom wind fence solutions are a versatile and durable way to mitigate wind and dust-related challenges across a variety of industries. By carefully assessing these factors, decision makers can make that lead to long-term success and operational efficiency.
References and Additional Reading Material:
- Osorio, R., Barden, C., Ciampitti, I. “GIS approach to estimate windbreak crop yield effects in Kansas-Nebraska” Agroforest System (2019) 93:1567-1576
- Grace, J. “Plant Response to Wind” Department of Forestry and Natural Resources University of Edinburgh. (1977) pp 36-40.
- Dabedan “Abrasion resistance and its importance in various applications” 23/04/2024 https://www.dabedan.com/en/abrasion-resistance-and-its-importance-in-various-applications-2/ Accessed January 13, 2025.
- Wikipedia “Knitted Fabric” https://en.wikipedia.org/wiki/Knitted_fabric Accessed January 13, 2025.
- Chowdhury, I., Summerscales, J., “Woven Fabrics for Composite Reinforcement: A Review” J. Compos. Sci 2024, 8(7), 2080; https://doi.org/10.3390/jcs8070280
- Dong, Z., Luo, W., Qian, G., et al. “Evaluating the optimal porosity of fences for reducing wind erosion” Sciences in Cold and Arid Regions 2011, 3(1): 0001-0012
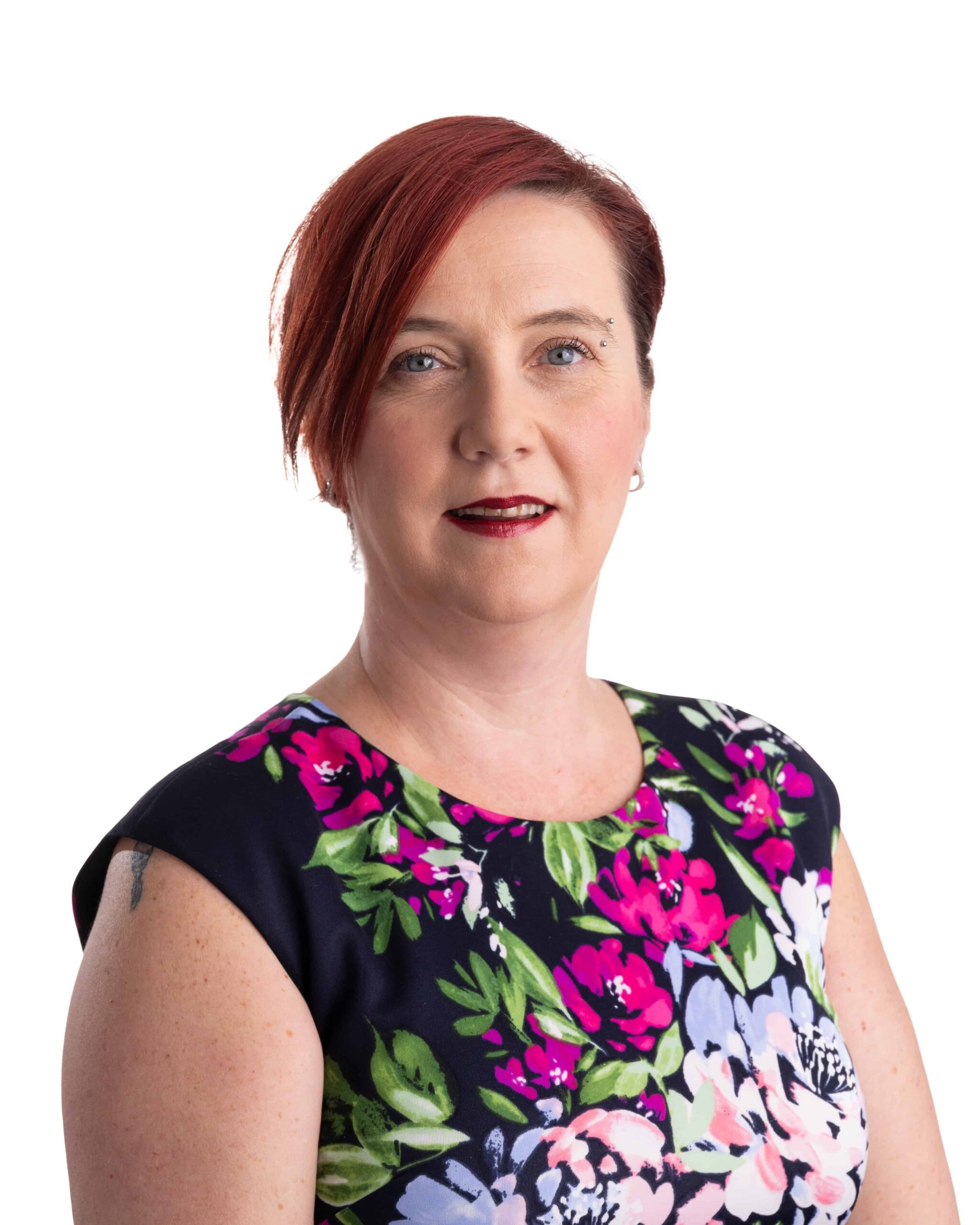
Claire Cowie is a seasoned Quality Assurance Manager with over two decades of experience in healthcare and manufacturing. Her career began in pharmacy, where she led teams and honed her skills in quality management systems. As she transitioned to the manufacturing sector, her unique background combines a deep understanding of policy and quality assurance with a keen eye for quality control.
Claire has been instrumental in implementing and cultivating a comprehensive quality control program within WeatherSolve Structures. She has successfully integrated her pharmaceutical background with manufacturing best practices, particularly in areas such as Good Manufacturing Practices (GMP) and ISO 9001 standards. Her unique blend of experience continues to drive innovation and excellence in her role.